How companies can pragmatically fulfill their due diligence obligations along the supply chain
Social Supply Chain
In global and increasingly complex supply chains, it is becoming more difficult to ensure transparency regarding working and social conditions along all stages of the value chain, especially in the case of widely dispersed supplier structures. Customers, legislators, and other stakeholders such as employees and credit institutions are increasingly insisting that companies adhere to social and ecological standards along the supply chain. As a result, this issue is also becoming a competitive factor for German and European companies.
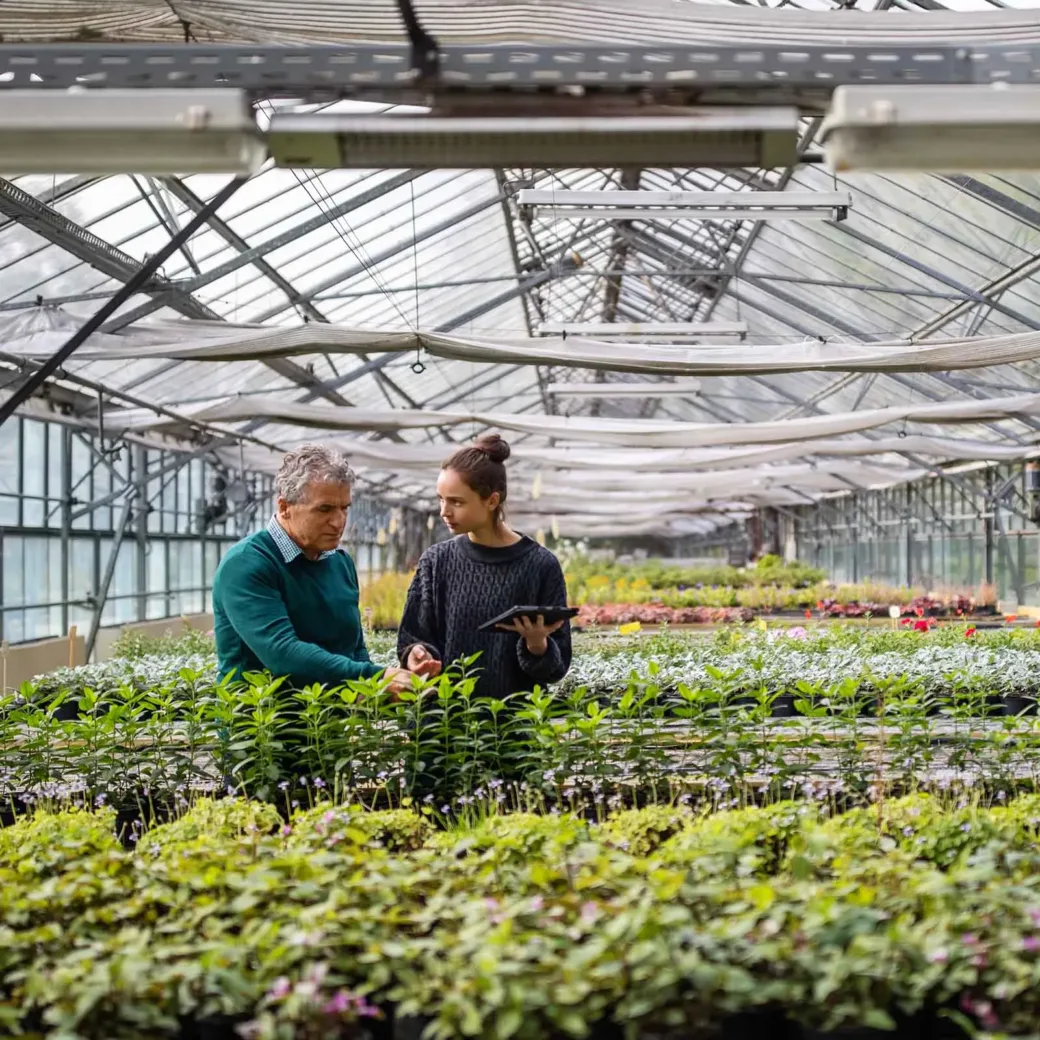
valantic helps you to pragmatically implement the requirements for social supply chains, whether due to legal regulations or stakeholder requirements. With our in-depth experience in sustainability as well as in purchasing and supply chain management, we are the ideal partner for making your supply chain end-to-end sustainable. We always ensure that all adjustments are integrated seamlessly into existing processes and systems in order to make the integration of sustainability requirements as efficient as possible.
We have proven our expertise time and again in numerous projects with dozens of satisfied customers. We are also happy to put you in touch with reference customers.
Supply Chain Due Diligence Act (LkSG)
Especially since the German Supply Chain Sustainability Act (Lieferkettensorgfaltspflichtengesetz or LkSG for short), many companies have had to deal with the social aspects of their own supply chain. We can help you to pragmatically integrate the requirements into your day-to-day business in order to protect your employees and resources.
Scope of application & legal requirements
The Supply Chain Act, which went into force on January 1, 2023, obliges companies to comply with human rights and environmental standards along their supply chains. This applies not only to activities within the company itself, but also to the business areas of suppliers and upstream suppliers at all stages of the supply chain. It therefore helps to ensure that production processes and working conditions in the supply chain that violate human rights can be traced so that targeted measures can be taken, and abuses eliminated.
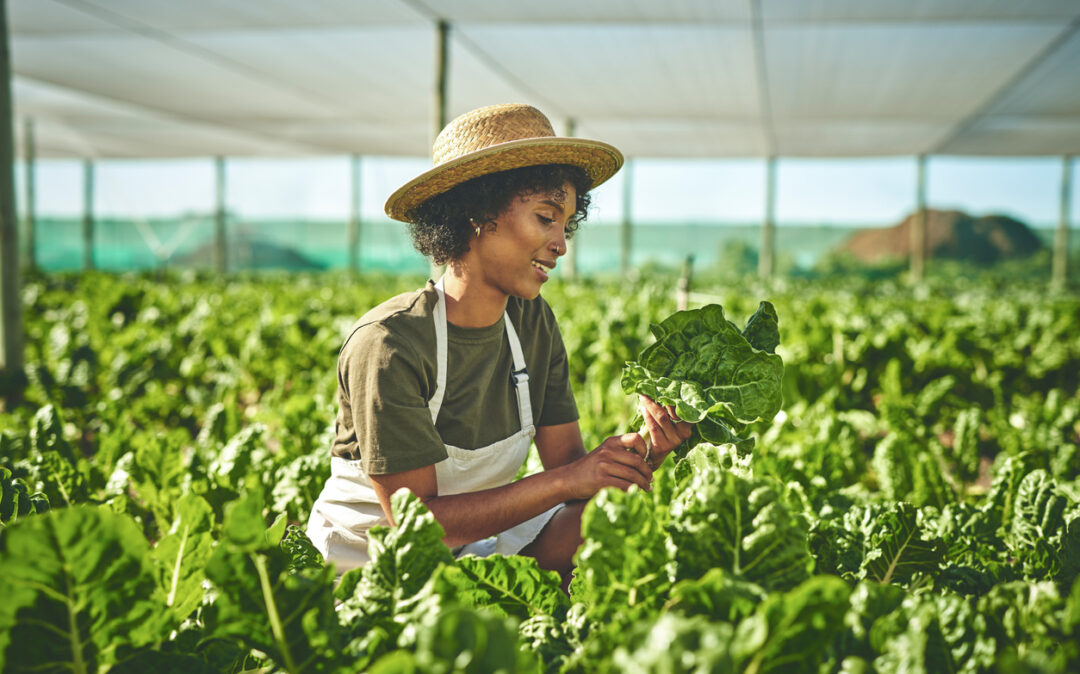
The LkSG is relevant for
- companies with more than 3,000 employees in Germany since January 2023
- also companies with more than 1,000 employees in Germany since January 2024
The legal regulations are explicitly designed to ensure that organizations take responsibility for their actions and reduce potential risks to the environment and employees.
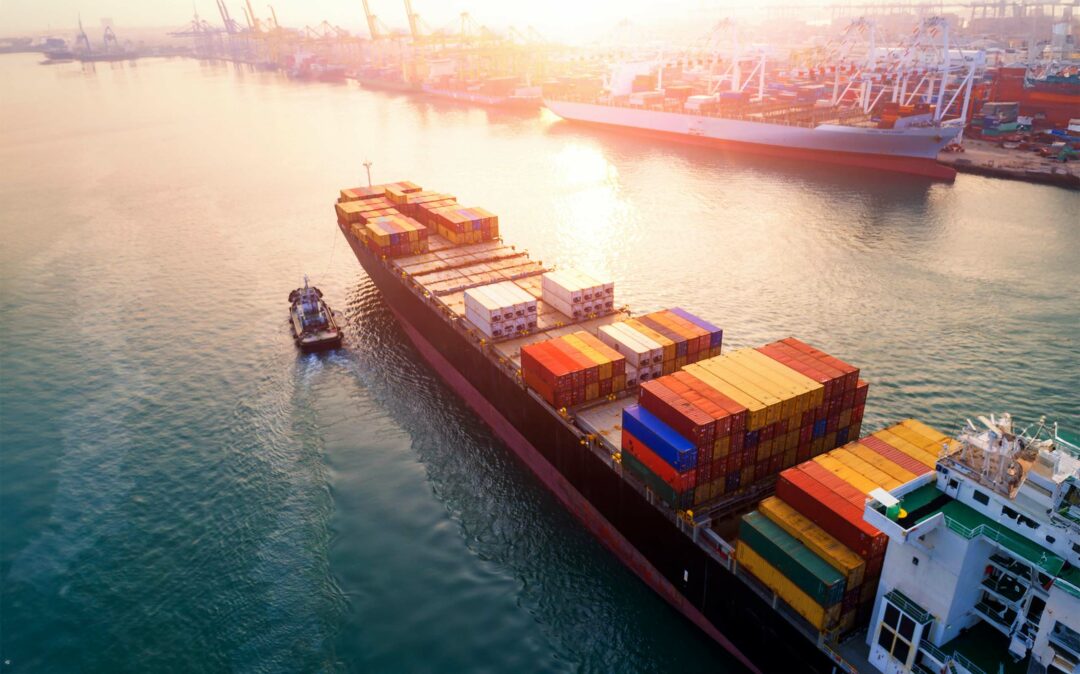
The law requires the following aspects
Establishment of a risk management system
Establishment of a comprehensive risk management system with regard to LkSG-relevant human rights and environmental risks (including responsibilities for operational implementation of due diligence obligations and monitoring of risk management)
Risk analyses in company's business area
Carrying out risk analyses with regard to the company’s own business area and direct suppliers
Complaints management system
Establishment of a complaints management system
Preventive measures against risks
Implementation of preventive measures to reduce potential risks (e.g. training, adaptation of purchasing practices, obtaining Supplier Code of Conduct)
Measures against existing risks
If necessary, implementation of remedial measures to immediately eliminate existing risks/violations
Publication of human rights strategy
Publication of the policy statement on the corporate human rights strategy
Reporting
Annual reporting to the responsible federal office
Implementation of the Supply Chain Act
It is advisable to implement the requirements of the Supply Chain Act in three steps in order to fulfill all due diligence obligations efficiently and step by step.
-
1
Readiness Check
First of all, a readiness check should be carried out to determine where the company currently stands and what still needs to be done to meet the LkSG requirements. To this end, existing documents (e.g. sustainability strategy, supplier code of conduct, supplier selection criteria) must be scrutinized critically. As the Supply Chain Act is a cross-departmental issue, it is advisable to involve all relevant departments at an early stage. The status quo of the company’s own activities and expectations should therefore also be discussed with the relevant stakeholders from different areas of the company (purchasing, compliance, management, sustainability, etc.). On this basis, a comparison can then be made with the legally required due diligence obligations (GAP analysis) and an implementation plan (compliance action plan) drawn up.
-
2
Risikoanalyse
In the second step, work should begin on defining the risk management system and carrying out risk analyses.
- In the risk management system, it is important to ensure that clear responsibilities for all due diligence obligations are clearly defined and recorded in process documentation. In addition, all LkSG-related information should come together at one point in the company, for example in the form of a LkSG coordination officer. This person can also implement some of the due diligence obligations themselves (e.g. writing the policy statement), but other due diligence obligations can also be implemented in a decentralized manner (e.g. external risk analysis or training). In addition to the implementation of due diligence obligations, the law also requires the definition of who is responsible for monitoring risk management. A separate role from the LkSG coordination officer should therefore take on the monitoring function in accordance with the dual control principle. The title “human rights officer” is mentioned by the law as an example but does not necessarily have to be used as such as long as it is also clearly defined under other titles who carries out which due diligence obligation and who monitors this.
- In the external risk analysis with regard to direct suppliers and service providers, the analysis is divided into two steps. First, an abstract risk analysis based on structured country and industry/product group risks must be carried out for all suppliers. The suppliers that have an increased risk based on their supplier country and industry/product group must then be considered individually and evaluated in the specific risk analysis. This is done, for example, by requesting relevant documents such as certifications or audits from the suppliers. If the risks are confirmed, preventive and, if necessary, corrective measures must be introduced.
There are a number of different tool providers that can assist with risk analysis. In addition to in-depth expertise in the establishment of common tools, valantic also provides its own pragmatic tool solutions within the scope of LkSG projects, which can be used by our customers independently and without follow-up costs or dependencies. - The internal risk analysis is also an integral part of the Supply Chain Act, in which the company’s own business area is reviewed with regard to the relevant risks. Here too, it makes sense to involve the relevant experts in all areas of the company. These include, for example, the occupational health and safety and environmental management officers as well as the HR and legal departments. In this way, the potential risks and how these are already being addressed and reduced by existing measures can be recorded in a structured manner. If there are still major residual risks, further risk mitigation measures must be introduced.
-
3
Results
Based on the risk management system and the results of the risk analyses, the third step is to close the remaining gaps in order to meet all legal requirements. This includes the creation and implementation of a training concept in the relevant business areas in which the identified risks are addressed or the creation of a policy statement on the corporate human rights strategy.
As it turns out, the introduction of the LkSG requirement can be very complex and time-consuming if you do not have extensive experience and best practices to fall back on. As experts in the introduction of the Supply Chain Act due diligence obligations with experience from dozens of projects with a wide range of customers from all industries, we can ensure that you implement the legal requirements pragmatically.
Our subject matter experts will be happy to talk to you with no obligation!
CSDDD – The European supply chain law
In March 2023, after long and tough negotiations, the CSDDD, the Corporate Sustainability Due Diligence Directive, was adopted. This means that from now on there will be a uniform supply chain law for all companies based or operating in Europe. The law therefore has a far-reaching impact on numerous companies and will significantly define future due diligence obligations in relation to their own supply chains.
Below you will learn how the scope of application of the CSDDD is defined, what measures are necessary, what potential sanctions may apply, and how you can make your company fit for the requirements of the European Supply Chain Act.
Scope of application and legal requirements
The directive applies to companies headquartered within the EU. It also includes companies that operate within the EU through their business activities. However, not all companies are affected equally. To mitigate the costs for small companies, the EU Commission has defined thresholds that will decrease continuously over a period of three years.
- Starting in 2027: companies with 5000+ employees and sales of €1.5 billion
- Starting in 2028: Companies with 3000+ employees and € 900 million in sales
- Starting in 2029: companies with 1000+ employees and € 450 million in sales
This means that around 1,450 companies in Germany and 5,300 companies throughout the EU will be directly affected by the new legislation.
Please note: Smaller companies are also likely to be indirectly affected by the CSDDD if they are a supplier to a directly affected company (e.g. automotive suppliers). The directly affected companies are likely to pass on parts of the disclosure and due diligence obligations to the supply chain. Therefore, early engagement with the requirements of the CSDDD today is a potential competitive advantage for the future.
Scope of application/depth of the supply chain
The European Supply Chain Act also represents an expansion of the scope of application in relation to the supply chain. Companies subject to the CSDDD are therefore subject to a detailed duty of care and reporting on activities in their own business area and in the supply chain.
Similar to the German Supply Chain Act (LkSG ), a comprehensive duty of care applies here.
In contrast to the LkSG, the CSDDD also requires the proactive consideration of activities in the deeper supply chain. This includes the activities of tier-n suppliers. However, the CSDDD does not require the analysis of all tier-1 to tier-n suppliers, but only those that are in the company’s “chain of activities.”
The EU thus describes those suppliers that are significantly responsible and necessary for the production of the goods or services of the reporting company. For a manufacturing company in France, for example, the suppliers of its Taiwanese chip manufacturer may very well be relevant, whereas the supplier of food and drink for the canteen does not fall under the scope of the CSDDD. In general, the law describes activities in the areas of design, mining, procurement, manufacturing, transportation, storage and supply of raw materials, materials, products, or parts of the product as relevant business activities.
However, each company must individually check which suppliers must be considered and which are not material.
In addition to monitoring suppliers, the CSDDD also requires the assessment of risks in the downstream supply chain. By definition, this includes activities in the areas of distribution, transportation, and storage. The entire issue of waste disposal was excluded from the obligation.
In the event of non-compliance with legal regulations or willful infringement, the CSDDD provides for relevant penalties for the companies concerned. These can amount to up to 5% of the company’s annual sales.
Civil liability is also explicitly anchored as an instrument in the CSDDD. However, clear conditions have been defined for this.
- In relation to demonstrable damage for which a company is responsible to a natural or legal person
- Only conditional on intent or negligence
- Burden of proof lies with the plaintiff
- NGOs can bring actions on behalf of victims
- The minimum limitation period is 5 years in any case
In contrast to earlier drafts, the possible exclusion from public procurement for the company was removed from the final law.
Implementation of the CSDDD at companies
The implementation of the CSDDD at companies is very similar to the requirements of the LkSG.
In certain aspects, however, the CSDDD differs from the LkSG. For example, the law prescribes a scoping approach for risk analysis. This provides for the following steps:
- Identifying the areas of the chain of activities where adverse impacts are most likely and severe
- Conducting detailed and in-depth assessments of individual suppliers in the prioritized areas
The law provides some guidance for prioritization by allowing probability and severity of adverse effects as criteria. However, aspects that were still frequently used in the LkSG are not permitted. These include expenditure or sales with the supplier in question, the supplier’s own leverage, and the duration of the collaboration.
Prioritization therefore becomes a decisive factor in the legally compliant implementation of the CSDDD. We are happy to assist you here.
In addition to the risk analysis, the CSDDD also deviates slightly from the directives of the LkSG in terms of preventive and corrective measures. As part of the European Supply Chain Act, it is also necessary to define your own share of existing or potential violations. Depending on the assessment, different options for action arise for companies.
In this case, the company must stop the behavior immediately and actively. Suitable measures must be defined and documented for this purpose. These must be reviewed for their effectiveness over time and adjusted, if necessary, until the risk has been eliminated.
If the company is involved in the infringement together with others, similar requirements apply as in the case of complete own fault. However, it is specifically mentioned that the company should primarily reduce its share of the risk.
If the company has become aware of breaches caused by a direct or indirect business partner, the company must use its leverage with the partner to bring about the cessation of the infringement. Here, it is crucial to define and document appropriate measures.
Your Contacts
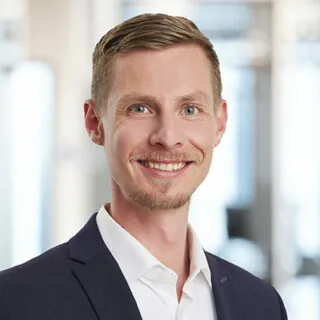
Marco Fuhr
Managing Consultant
valantic Supply Chain Excellence
- Decarbonization
- Social Supply Chain
- Twin Transition
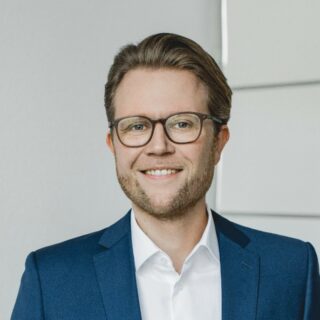
Jan Laakmann
Chief Operating Officer
HÖVELER HOLZMANN – a valantic company
- Sustainability strategy & roadmap
- ESG reporting (CSRD)
- Social supply chains (LkSG, EUDR, CBAM)
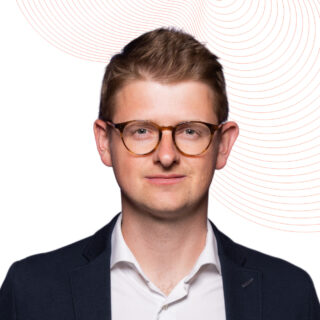
Dr. Jens Lehnen
Principal
valantic NXT GmbH
- Sustainability strategy & roadmap
- Circular Economy
- Green IT
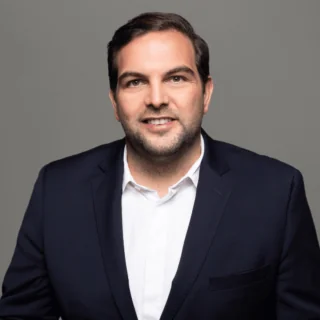
Sebastian Badaghlou
Partner
valantic Digital Finance
- Digital Finance
- Financial Steering
- Corporate Perfomance Management
- Financial Consolidation