Nordic Rail Service GmbH
IT-based service process as a starting point for digitalization
Together with valantic, Nordic Rail Service GmbH has implemented a digitalized service process based on SAP. 50 employees receive all information on an order, broken down by service type.
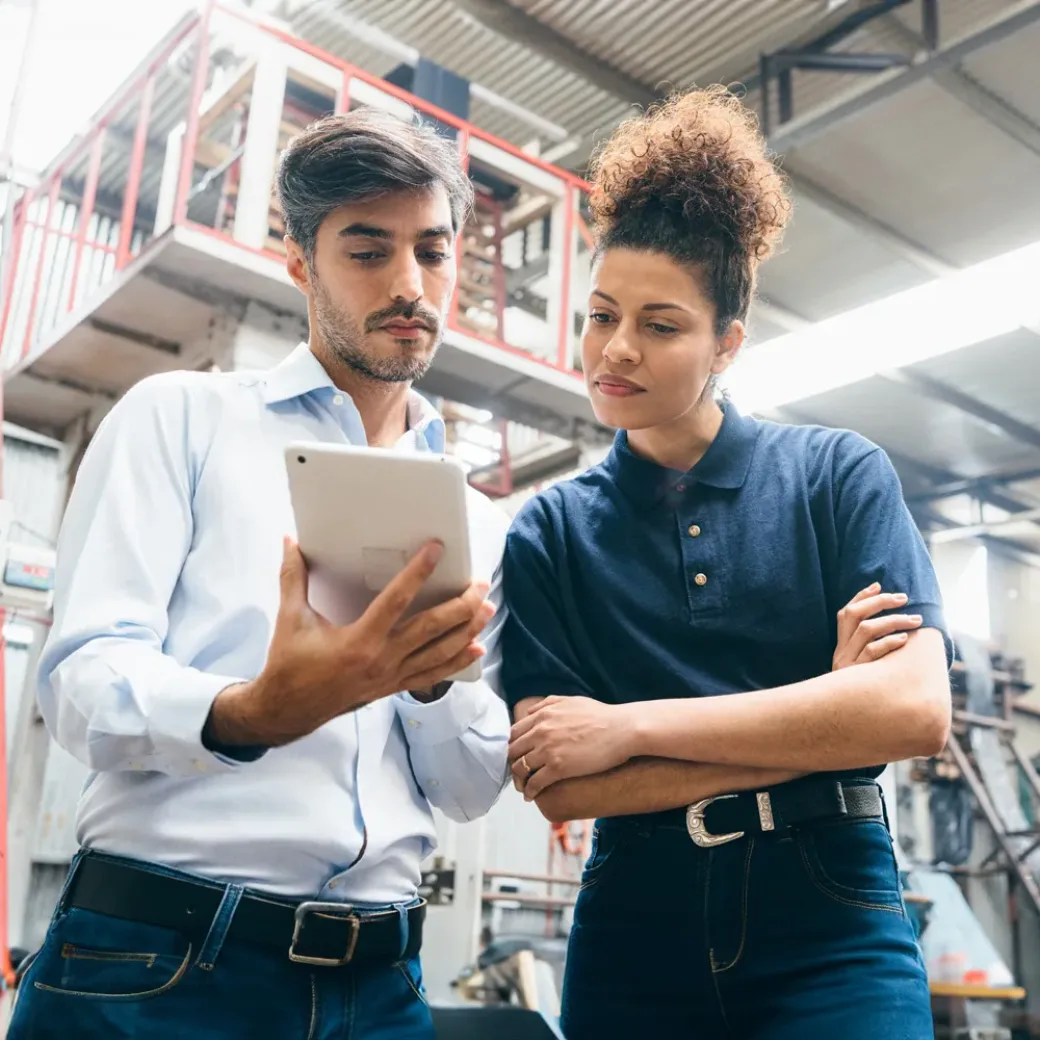
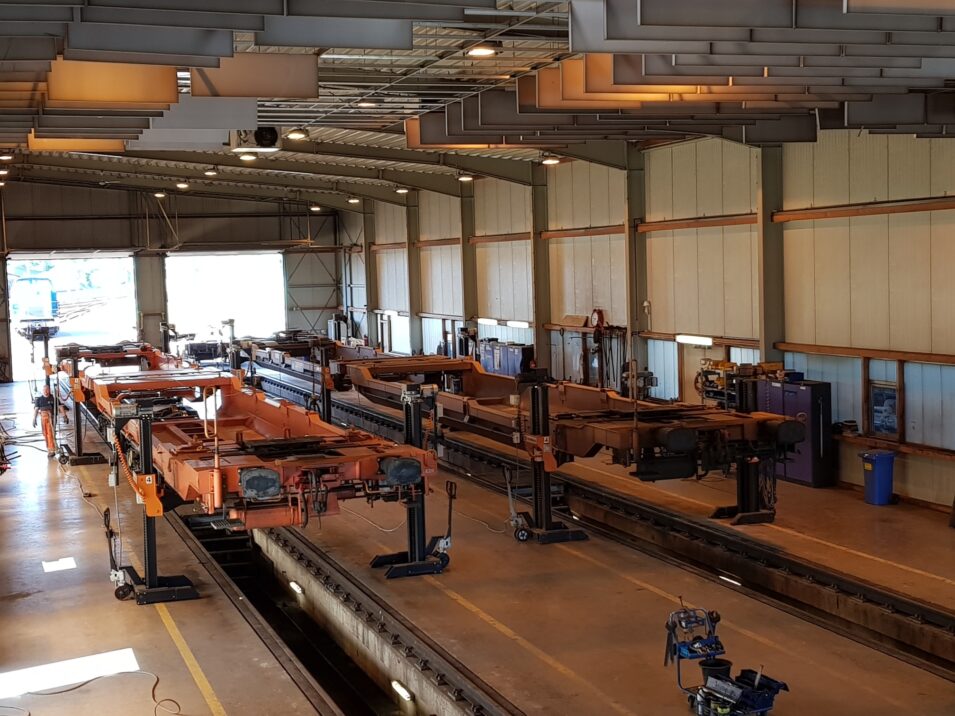
About Nordic Rail Service GmbH
Nordic Rail Service GmbH (NRS) is a company in the Lübecker Hafen-Gesellschaft mbH (LHG) group and was founded in 2003 with the construction of the freight car workshop. LHG is Germany’s largest RoRo port on the Baltic Sea and operates parts of the port here with the Skandinavienkai in Travemünde, the Seelandkai, Schlutup and the Nordlandkai near the city center. The rail transport division (EVU) provides wagon masters, shunting personnel, pilots and train drivers. NRS operates short and medium-haul services with a fleet of diesel locomotives in the 600, 1,000, 2,000 and 4,000 kW power classes.
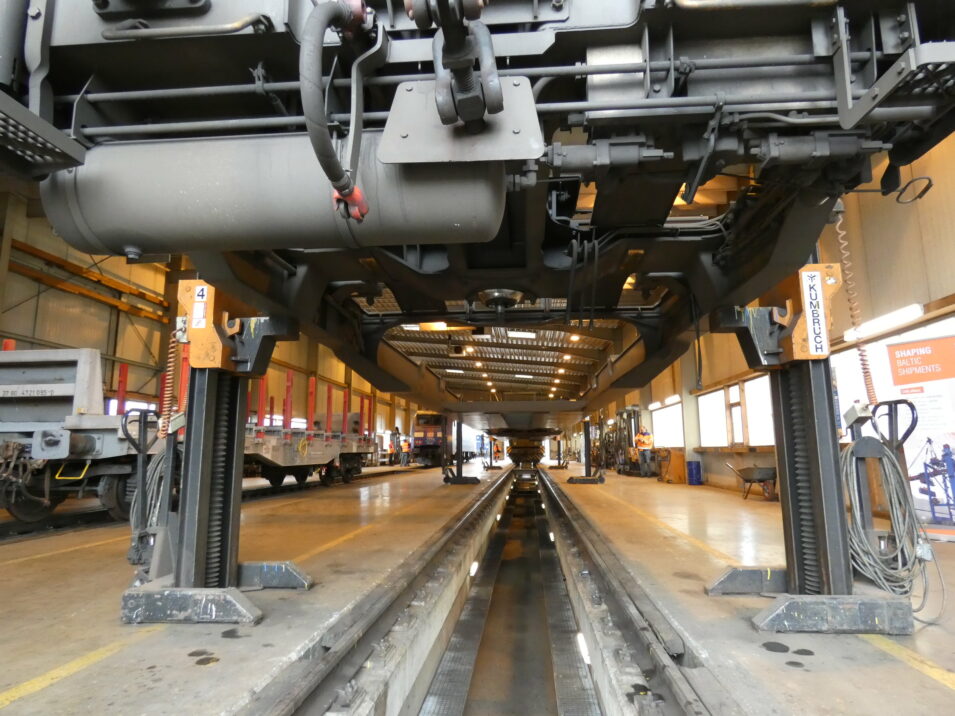
The challenge
In order to transport the cargo to and from the ships, seven NRS GmbH diesel locomotives run on a 60 km long rail network between the port terminals, the individual company sidings and the Deutsche Bahn lines. These not only shunt the freight wagons with the load, but also pull the wagons over short and medium distances. NRS also looks after the tracks and signals in and around Lübeck and carries out stationary maintenance work on its own and third-party freight wagons in a workshop and on the move.
Excel is not yet digitization
The maintenance of third-party wagons is often carried out on behalf of a freight wagon lessor that leaves its wagons to rail transport companies. “In the past, we organized the entire service process to a large extent with pen and paper,” says Thomas Toschka, Head of Division and EBL. The data for many steps along the process was initially recorded manually and then had to be subsequently transferred to SAP ERP. This worked, but was time-consuming and error-prone. In addition, more and more NRS customers – i.e. the freight wagon rental companies – were requesting that the service process be handled digitally. Thomas Toschka comments: “As a small rail transport company, we were still at the beginning of the digital transformation – and not just in terms of service. We were already using SAP ERP for accounting, but calculations were created using Microsoft Excel. But that’s not digitalization yet.”
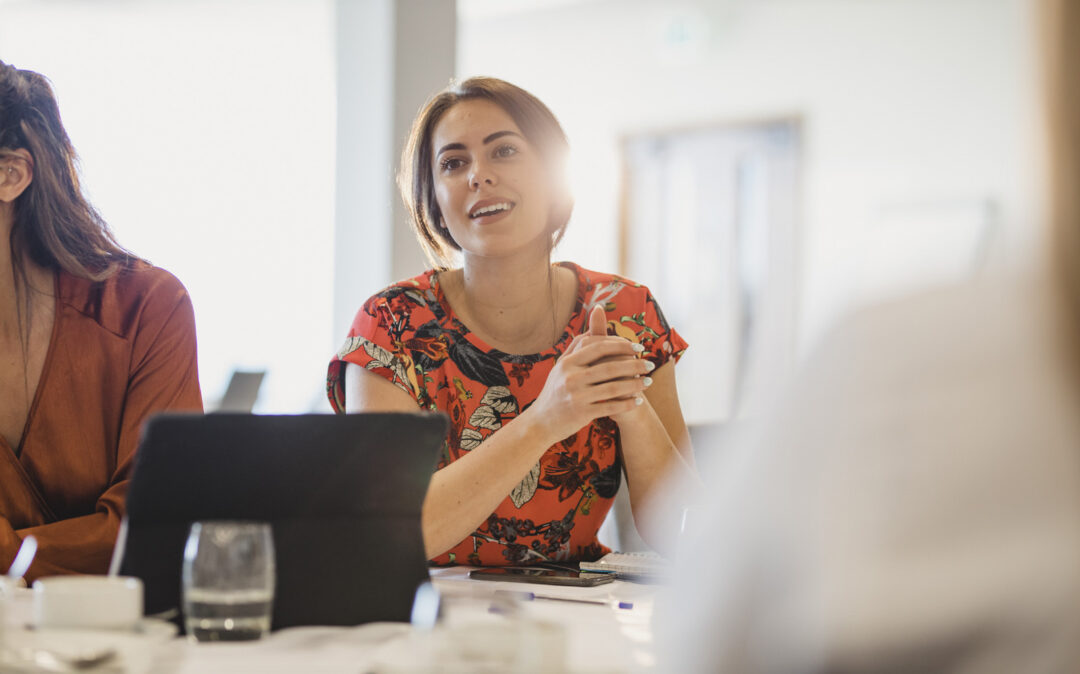
Lübeck, Germany
Location
5
Employees
Shunting, maintenance of freight wagons
Portfolio
The solution
Decision in favor of valantic as a trusted partner
For this reason, those responsible at NRS decided to digitally map the entire service process – and thus simultaneously create the basis for a holistic digitalization of maintenance and the other business areas. An important requirement was that the software for the service process could be connected to SAP ERP. With the software that Nordic Rail Service initially had in mind, this would have involved considerable effort in connecting the maintenance software to the SAP system. There was therefore a desire to represent the maintenance processes within SAP ERP. For this reason, the company ultimately decided to use the existing SAP system and develop it accordingly.
Once the decision had been made in favor of SAP as the software, it was immediately clear that Orianda Solutions AG – a valantic company was the right partner for the implementation. “I first came across Orianda a few years ago at a seminar on the digitalization of maintenance,” says Thomas Toschka. “The Swiss Federal Railways had reported on a joint project with Orianda Solutions AG – a valantic company. That was a hugely valuable tip for me.”
“Until then, we had searched in vain for a partner who was familiar with both the maintenance of rail vehicles and SAP. So we didn’t have to think long about who we wanted to digitize the service process with,” says Thomas Toschka, Head of Division and EBL.
Trusting and pragmatic collaboration
In a workshop, the requirements of NRS were first clearly identified together and a rough concept was drawn up. In principle, NRS could have gone to another consultancy. Thomas Toschka: “However, there was no reason for us to do so, as we were even more convinced of Orianda’s expertise after the workshop. What’s more, they were also a perfect match on a personal level.”
Just how well the two partners were able to work together became apparent over the course of the project, as new challenges arose from time to time that were not foreseen in the original scope. For example, the desire to integrate a ZUG-FeRD interface only arose after some time. Thanks to the trusting and pragmatic cooperation and the agile approach, such adjustments were implemented and mastered well.
From the damage report to the invoice
Following the successful introduction and customization of the SAP ERP modules Customer Service (CS), Plant Maintenance (PM) and Sales and Distribution (SD), billing-relevant data and documents can now be exchanged throughout the service process without media discontinuity. This begins when an order is created in the Customer Services module – either when a hiring company returns a wagon or when the order is placed by the freight wagon hire company itself. To create an order, employees can access stored elements: the line codes (the industry standard and individual customer codes) and the execution quantity, own material and customer material as well as flat rates and text items. If a hired wagon is returned, NRS also creates a damage report, assigns it to the order and sends it to the customer. If maintenance is carried out in the track field, a Fiori-based app is used to record all damage in the Plant Maintenance module. Particularly advantageous: UIC numbers and AVV codes can be accessed and comments and images can be easily added.
Once the order has been fully created, a quotation can be generated from it with just a few clicks, taking into account the customer-specific hourly rates and material prices. The services, materials and flat rates are summarized in the quote according to service types and shown with corresponding subtotals, providing the customer with an optimal overview. NRS only begins maintenance of the freight wagon once an offer has been confirmed. The time actually spent during the measure is continuously recorded via SAP CATS (Cross Application Time Sheet) and the material used is documented using a scanner.
Once the maintenance has been completed, the order is first used to generate an invoice request in the Customer Service module and then an invoice in the Sales and Distribution module. The services, materials and flat rates are also grouped by service type in the invoice. The invoice can be transmitted in ZUG-FeRD format – but of course also as a PDF document or as a paper invoice, as required.
Goal
- Establishment of an end-to-end digitalized service process that meets the requirements of customers – i.e. freight wagon rental companies
- Transmission of invoices – broken down by service type (service codes, materials and customer materials) – to customers in ZUGFeRD format
- Increased efficiency in handling the service process and minimized susceptibility to error
The solution
- Implementation or customizing of the SAP ERP modules Customer Service (CS), Plant Maintenance (PM) and Sales and Distribution (SD)
- Development of individual components
- Creation of forms in the Sales and Distribution module
Benefit
- Improving customer satisfaction and customer loyalty
- Ensuring future viability
Plans for the future
By introducing and customizing the SAP modules Customer Service, Plant Maintenance and Sales and Distribution, Nordic Rail Services was able to establish a service process that meets all of the customer’s requirements. But this is just the beginning. In the future, pen and paper are to disappear completely from the maintenance process. The aim is to create a fully digitalized maintenance process.
To this end, Nordic Rail Services has now recorded and documented all processes and checked how they are already mapped or could be mapped using SAP. The existing gaps are to be successively closed. For example, those responsible are considering mobile solutions for the asset creation of an order and the execution of a maintenance measure. It is also conceivable to connect customers’ systems in order to import ZUG-FeRD invoices. There is also potential in the automatic recording and transmission of vehicle data for freight wagons.
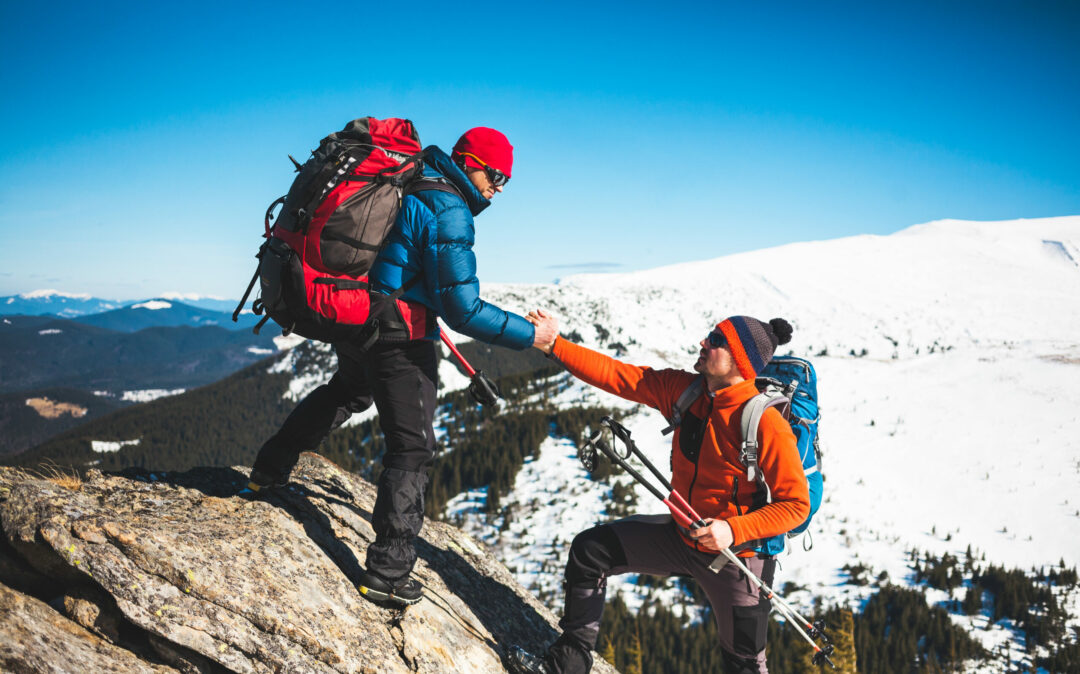
Your Contact
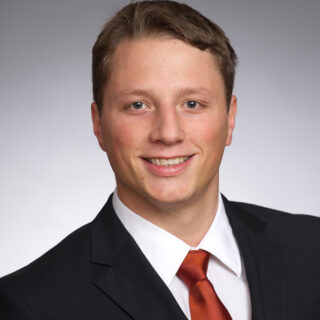
Felix Schott
Consultant Manager
Orianda Solutions AG - a valantic company