Im neuen Betriebsgebäude im niedersächischen Vreden plant Schmitz Cargobull, pro Tag 100 Kühl- und Trockenfrachtfahrzeuge fertigzustellen. Der Baubeginn startet im ersten Halbjahr 2025. Die 4.500 Quadratmeter große Werkserweiterung für den Ausbau der Produktionskapazitäten für Kühlauflieger und Kofferfahrzeuge ist dem Unternehmen eine Investition von 50 Millionen Euro wert.
Zentraler Bestandteil dieses Projekts ist der Einsatz digitaler Werkzeuge bei der Planung der neuen Gebäude und Anlagen. Für zukünftige Produktionsabläufe werden digitale Simulationen durchgeführt, um die neuen Prozesse frühzeitig zu testen und abzusichern. Damit nicht genug. Neben der neuen Fertigungshalle wird auch ein neues Logistikkonzept eingeführt, um die internen Abläufe weiter zu verbessern. Darüber hinaus wird die schrittweise Modernisierung der Komponentenfertigung vorangetrieben.
„Neu ist, dass wir unsere Fabrik digital und integriert planen. Wir wollen die Potenziale der digitalen Transformation in unserer Fertigung nutzen.“
Stefan Cramer, Werksleiter bei Schmitz Cargobull
Der Einsatz digitaler Werkzeuge bei der Planung der neuen Gebäude und Anlagen hat eine deutlich verbesserte Gestaltung der Arbeitsprozesse zum Ziel. „Neu ist, dass wir diese Fabrik digital und integriert planen. Das ist die größte Herausforderung. Wir wollen die Potenziale der digitalen Transformation in unserer Fertigung nutzen“, sagt Stefan Cramer, Werksleiter bei Schmitz Cargobull.
Taktzeiten von 15 auf 10 Minuten reduzieren
Durch die Einführung moderner digitaler Technologien soll die Produktionskapazität deutlich gesteigert werden. So gilt es, die Anzahl der pro Schicht gefertigten Kühlfahrzeuge auf 40 zu erhöhen und zugleich durch den verstärkten Einsatz von Automatisierung und Digitalisierung die Taktzeit pro Trailer von derzeit 15 auf 10 Minuten zu verringern.
Schon in der Planung werden nach Angaben Cramers für die zukünftigen Produktionsabläufe digitale Simulationen durchgeführt, um die neuen Prozesse ausführlich auf Praxistauglichkeit zu testen. Dabei sind nicht nur Einzelaspekte zu beachten, „sondern integrativ die ganze Fabrik – von der Planung über den Betrieb bis zur Versorgung mit Material. Es geht um einen ganzheitlichen Ansatz. Wir müssen alte Denkmuster aufgeben und ganz neue Felder erschließen“, betont der Werksleiter.
Das bedeutet, die Gebäude, Fertigungsbereiche, Linien, Arbeitsplätze und Anlagen schon vor der Realisierung digital darzustellen. „Bisher haben wir das noch nicht gemacht“, sagt Cramer. Zwar habe das Unternehmen bereits einzelne Gebäude digital geplant oder 2D- oder 3D-Planungen für Anlagen umgesetzt. Aber in einem Modell haben wir das noch nicht integriert.“
Ziele: Produktivität erhöhen, Fehler vermeiden, Kosten senken
Doch nun geht es ums Ganze: Von der Fabrikplanung, der Planung der Arbeitsplätze bis zu allem, was mit dem Thema Manufacturing zu tun hat. Zu beachten sind auch Vorbereitung und Durchführung der Arbeit, Qualität und Instandhaltung sowie die Logistik und Steuerung der Lieferketten und dem Materialfluss im Werk. Zudem sollen KI-Anwendungen zum Einsatz kommen, um das Manufacturing technologisch auf ein neues Level bringen, mithin eine höhere Produktivität zu erreichen, Fehler zu vermeiden und Kosten zu senken. Dazu gehört auch, dass bei der Logistik die Materialversorgung schlanker wird. Denn so lassen sich Bestände in den Prozessen verringern und kürzere Reaktionszeiten einführen. Und schließlich sollen auch Transporte und damit CO2-Footprints gesenkt werden. „Das sind die Ergebnisse, die wir uns erhoffen“, betont Cramer.
Investitionen von mehr als 1 Billion Euro weltweit
Nach dem Modell des Trailer-Herstellers wollen auch andere Unternehmen auf die Digitale Fabrik setzen. So planen Industrieunternehmen weltweit jährlich über eine Billion Euro in digitale Transformationslösungen zu investieren, wie die Studie „Digital Factory Transformation Survey“ von PwC erhoben hat. Eine digitale Fabrik soll „die Agilität des Unternehmens steigern und ihm dadurch einen Wettbewerbsvorteil verschaffen. Sie repräsentiert das Optimum der digitalen Transformation in der Fertigung“, sagt Detlev Reicheneder, Senior Director, Business Strategy Design and Manufacturing bei Autodesk in Deutschland.
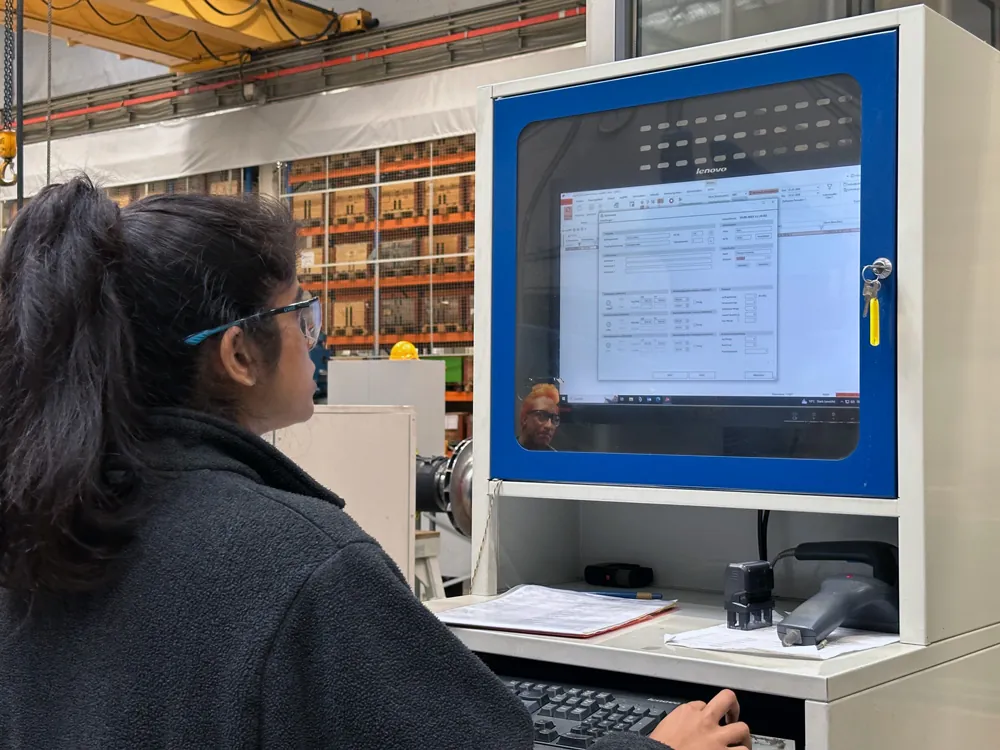
Allerdings ist das Tempo noch verhalten, wie Experten des „IPH – Institut für Integrierte Produktion Hannover“ beobachten. Der Übergang zur Digitalen Fabrik bewege sich nur schrittweise. Ein Muster sei jedoch bereits erkennbar: Zunächst setzen Unternehmen branchenspezifische Anforderungen um. Anschließend folgen allgemeine Anwendungen wie die Planung der Gesamtfabrik oder der Logistik.
Als Werkzeug wird das dreidimensionale CAD-Modell der Fabrik-Layout-Gestaltung verwendet. Dieses virtuelle Fabrikabbild wird in der digitalen Fabrikplanung von Virtual- und Augmented Reality-Lösungen genutzt. Auf diese Weise lässt sich die Fabrik schon in der Planungsphase virtuell begehen. Außerdem sind visuelle Details wie die Aufstellung der neu geplanten Maschinen in der Fertigungshalle darstellbar.
Must-haves bei der digitalen Fabrik-Planung
Zudem werden Tools wie das Projekt- und Wissensmanagement oder das „computer aided office“ im Gesamtprozess von der Produktentwicklung über die Produktionsplanung bis zum Betrieb eingesetzt. Sie unterstützen beim elektronischen Datenaustausch und der Weitergabe von Wissen und Informationen. Weitere Werkzeuge sind die Ablaufsimulation für Produktionsplanung und -betrieb, die virtuelle Inbetriebnahme vor dem Hochfahren der Anlagen oder ein Enterprise Resource Planning (ERP) System zur Planung von Aufgaben und Ressourcen.
Eine unternehmensübergreifende Methode zur Planung und Verwirklichung der Digitalen Fabrik ist das „simultaneous engineering“. Dabei wird die Entwicklung auf mehrere parallel arbeitende Teams verteilt, wodurch sich die gesamte Entwicklungszeit erheblich verkürzt. Realisierbar ist die simultane Bearbeitung durch digitale Modelle, die stets aktuell und für die Projektteilnehmer einsehbar sind. Die Erstellung und Verwaltung dieser Modelle wird vom Produkt- und Simulationsdatenmanagement gesteuert.
Allerdings müssen Unternehmen, die den Weg in Richtung Digitale Fabrik einschlagen wollen, erstmal einen soliden Datenbestand einrichten. Das ist ist die Basis für weiteres Handeln. Echte Hindernisse sind nach Beobachtung der IPH-Experten mangelnde Planungsgrundlagen. So verfügen die meisten KMU beispielsweise über keine aktuellen Fabriklayouts oder Datenerfassungssysteme an ihren Maschinen. Zudem fehlen auch 3D-Produkt- und Fabrikdaten, wie beispielsweise die Medienversorgung oder auch die Pufferlagergrößen.
Diese Vorteile bringt die Digitale Fabrik
Selbstorganisierte Fabrik: Die Digitale Fabrik bildet mit ihren virtuellen Modellen die Grundlage für die Erstellung und Inbetriebnahme der Smart Factory. Das ist eine Produktionsumgebung, in der sich Fertigungsanlagen und Logistiksysteme selbst organisieren.
Mit Hilfe der Digitalen Fabrik lassen sich verschiedene Szenarien simulieren. Die Vernetzung von Anlagen und Systemen ist eine Seite der Smart-Factory-Strategie. Auf der anderen Seite sind auch die Produkte mit maschinell lesbaren Informationen wie beispielsweise RFID-Chips oder QR-Codes ausgestattet. Durch den Informationsfluss und die Vernetzung der gesamten Fertigung ist eine „Losgröße 1 Produktion“ möglich.
Datenbasis und Schnittstellen: Bei der Umsetzung einer Smart Factory kommt es auf die Auswahl und Konfiguration geeigneter Schnittstellen zwischen den unterschiedlichen Systemen und Werkzeugen an. Das Datenformat und Datenprotokoll beeinflusst den Aufwand bei der Erststellung und beim Betrieb von digitalisierten Lösungen.
To-dos für die Zukunft: Ein vollständig digitales Abbild der Fabrik, das für den Einsatz digitaler Werkzeuge und Methoden genutzt werden kann, ist für kleinere und mittlere Unternehmen (KMU) noch nicht erreichbar. Auch größere Unternehmen und Konzerne haben noch nicht alle Prozesse digitalisiert oder ein komplettes digitales Abbild erstellt. Voraussetzungen wie eine 3D-CAD-Fabrikplanung sind bei einigen größeren Unternehmen jedoch bereits vorhanden.
(Quellen: IPH – Institut für Integrierte Produktion Hannover gGmbH, eigene Recherche)